Nickel-based alloy .(HY-industry technique center)
Nickel-based alloy refers to a kind of alloy which has high strength and certain anti-oxidation and corrosion resistance at 650-1000 °C. According to the main main properties, it is subdivided into nickel-based heat-resistant alloy, nickel-based corrosion-resistant alloy, nickel-based wear-resistant alloy, nickel-based precision alloy and nickel-based shape memory alloy. Superalloys are classified into iron-based superalloys, nickel-based superalloys and cobalt-based superalloys according to the matrix. Among them, nickel-based superalloys are referred to as nickel-based alloys.
Representative materials for nickel-based alloys are: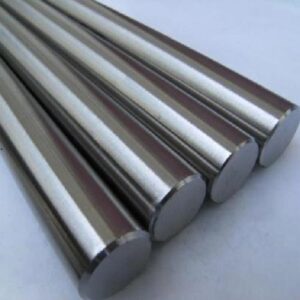
-
Incoloy alloy, such as Incoloy800, the main component is; 32Ni-21Cr-Ti, Al; is a heat resistant alloy;
-
Inconel alloy, such as Inconel600, the main component is; 73Ni-15Cr-Ti, Al; is a heat resistant alloy;
-
Hastelloy alloy, that is, Hastelloy, such as Hastelloy C-276, the main component is; 56Ni-16Cr-16Mo-4W; is a corrosion-resistant alloy;
-
Monel alloy, that is, Monel, such as Monel 400, the main component is; 65Ni-34Cu; is a corrosion-resistant alloy;
Main alloying element
-
The main alloying elements are chromium, tungsten, molybdenum, cobalt, aluminum, titanium, boron, zirconium and the like. Among them, Cr, Ai and the like mainly play an antioxidant role, and other elements have solid solution strengthening, precipitation strengthening and grain boundary strengthening.
-
It has high strength and certain anti-oxidation ability at 650~1000°C. It is widely used in the manufacture of aero-engine blades and rocket engines, nuclear reactors and energy conversion equipment due to its high temperature strength and oxidation resistance. High temperature parts.
Development History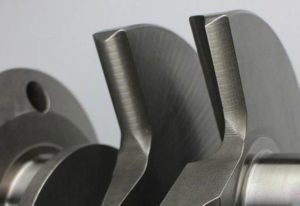
-
Nickel-based superalloys (hereinafter referred to as nickel-based alloys) were developed in the late 1930s. In 1941, the United Kingdom first produced a nickel-based alloy Nimonic 75 (Ni-20Cr-0.4Ti); in order to increase the creep strength and added aluminum, Nimonic 80A (Ni-20Cr-2.5Ti-1.3Al) was developed. In the mid-1940s, the Soviet Union developed nickel-based alloys in the late 1940s in China in the mid-1940s. The development of nickel-based alloys includes two aspects: improvements in alloy composition and innovation in production processes. In the early 1950s, the development of vacuum smelting technology created conditions for the refining of nickel-based alloys containing high aluminum and titanium. The initial nickel-based alloys are mostly deformed alloys. In the late 1950s, due to the increase of the working temperature of the turbine blade, the alloy was required to have higher high temperature strength, but the strength of the alloy was high, it was difficult to deform or even deform, so the investment casting precision casting process was used to develop a series of good High temperature strength casting alloy. In the mid-1960s, more oriented crystallization and single crystal superalloys and powder metallurgy superalloys were developed. In order to meet the needs of ships and industrial gas turbines, a number of high-chromium-nickel-based alloys with good thermal corrosion resistance and stable structure have been developed since the 1960s. In the 40 years from the early 1940s to the end of the 1970s, the operating temperature of nickel-based alloys increased from 700 ° C to 1100 ° C, an average increase of about 10 ° C per year.
Composition and performance
-
Nickel-based superalloys are the most widely used. The main reason is that, in the nickel-based alloy, more alloying elements can be dissolved and the structure stability can be maintained. Secondly, the coherently ordered A3B intermetallic compound γ[Ni3(Al,Ti)] can be formed. As a strengthening phase, the alloy is effectively strengthened to obtain higher high temperature strength than iron-based superalloys and cobalt-based superalloys; third, chromium-containing nickel-based alloys have better oxidation resistance and resistance than iron-based superalloys. Gas corrosion capacity. Nickel-based alloys contain more than ten elements, of which Cr mainly acts as an antioxidant and anti-corrosion, and other elements mainly play a reinforcing role. According to their strengthening mode, they can be divided into solid solution strengthening elements such as tungsten, molybdenum, cobalt, chromium and vanadium; precipitation strengthening elements such as aluminum, titanium, niobium and tantalum; grain boundary strengthening elements such as boron and zirconium. Magnesium and rare earth elements.
classification
-
The nickel-based superalloy has a solid solution strengthening alloy and a precipitation strengthening alloy in a strengthened manner.
Production Process
-
In terms of smelting: in order to obtain more pure molten steel, reduce the gas content and harmful element content; at the same time, due to the presence of easily oxidizable elements such as Al, Ti, etc. in some alloys, non-vacuum smelting is difficult to control; more is to obtain better thermoplasticity. Nickel-based heat-resistant alloys are usually smelted in a vacuum induction furnace, and even produced by vacuum induction smelting plus vacuum self-consumption furnace or electroslag furnace remelting.
-
In terms of deformation: the forging and rolling process is adopted, and the alloy with poor thermoplasticity is even rolled by extrusion or directly extruded by mild steel (or stainless steel). The purpose of the deformation is to break the cast structure and optimize the microstructure.
-
Casting: The mother alloy is usually smelted in a vacuum induction furnace to ensure the composition and control gas and impurity content, and the parts are made by vacuum remelting-precision casting.
-
For heat treatment: deformed alloys and partially cast alloys are subjected to heat treatment, including solution treatment, intermediate treatment and aging treatment. Taking Udmet 500 alloy as an example, its heat treatment system is divided into four sections: solution treatment, 1175 ° C, 2 hours, Air cooling; intermediate treatment, 1080 ° C, 4 hours, air cooling; one aging treatment, 843 ° C, 24 hours, air cooling; secondary aging treatment, 760 ° C, 16 hours, air cooling. Get the required tissue status and good overall performance.
Nickel based corrosion resistant alloy
-
The main alloying elements are copper, chromium and molybdenum. Has a good overall performance, resistant to a variety of acid corrosion and stress corrosion. The earliest application (produced in the United States in 1905) is nickel-nickel (Ni-Cu) alloy, also known as Monel alloy (Monel alloy Ni 70 Cu30); in addition, nickel-chromium (Ni-Cr) alloy (that is, nickel-based heat-resistant alloy) , the heat-resistant corrosion alloy in the corrosion-resistant alloy), nickel-molybdenum (Ni-Mo) alloy (mainly referred to as Hastelloy B series) domestic professional corrosion-resistant alloy manufacturer has Beijing Iron and Steel Research Institute, Shanghai HY Industry Co., Ltd., Baoti Group Rare Metal Materials Co., Ltd., Ni-Cr-Mo alloy (mainly referred to as Hastelloy C series, domestic professional corrosion-resistant alloy manufacturer has Beijing Iron and Steel Research Institute, Shanghai HY Industry Co., Ltd, Bao Titan Group Rare Metal Materials, etc.). At the same time, pure nickel is also a typical representative of nickel-based corrosion-resistant alloys. These nickel-based corrosion-resistant alloys are mainly used in the manufacture of various corrosion-resistant environmental parts such as petroleum, chemical, and electric power.
Category:
Nickel-based corrosion resistant alloys have austenitic structures. In the solid solution and aging treatment state, there are also intermetallic phases and metal carbonitrides on the austenite matrix and grain boundaries of the alloy. The various corrosion resistant alloys are classified according to their composition and their characteristics are as follows:
-
Ni-Cu alloy(For example:monel400,monel K500) has better corrosion resistance than nickel in reducing medium, and corrosion resistance is better than copper in oxidizing medium. It is high temperature resistant fluorine gas, hydrogen fluoride and hydrogen fluoride under the conditions of no oxygen and oxidant. The best material for acid (see metal corrosion).
-
Ni-Cr alloy is also a nickel-based heat resistant alloy; it is mainly used under oxidizing medium conditions. Corrosion resistance to high temperature oxidation and corrosion of gases such as sulfur and vanadium increases with the increase of chromium content. These alloys also have good resistance to corrosion by hydroxides (such as NaOH, KOH) and resistance to stress corrosion.
-
The Ni-Mo alloy is mainly used under the conditions of corrosion of a reducing medium. It is the best alloy for hydrochloric acid corrosion, but corrosion resistance is significantly reduced in the presence of aerobic and oxidizing agents.
-
The Ni-Cr-Mo (W) alloy combines the properties of the above Ni-Cr alloy and Ni-Mo alloy. It is mainly used under the conditions of oxidation-reduction mixed medium. Such alloys have good corrosion resistance in high temperature hydrogen fluoride, in hydrochloric acid containing oxygen and oxidizing agents, hydrofluoric acid solution, and in wet chlorine at room temperature.
-
Ni-Cr-Mo-Cu alloy has the ability to resist both nitric acid and sulfuric acid corrosion, and also has good corrosion resistance in some oxidation-reduction mixed acids.
Nickel based wear resistant alloy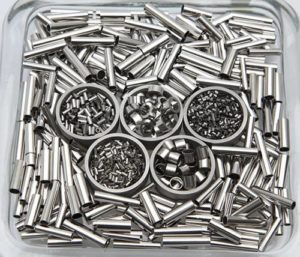
The main alloying elements are chromium, molybdenum, tungsten, and also a small amount of antimony, bismuth and indium. In addition to its wear resistance, it is also resistant to oxidation, corrosion and welding. It can be used to manufacture wear-resistant parts or as a coating material, which can be coated on the surface of other base materials by surfacing and spraying processes.
The nickel-based powder has a self-fluxing alloy powder and a non-self-fluxing alloy powder.
-
The non-self-fluxing nickel-based powder means a nickel-based alloy powder containing no B, Si or B, and a low Si content. These powders are widely used in plasma arc spray coatings, flame spray coatings and plasma surface strengthening. Mainly include: Ni-Cr alloy powder, Ni-Cr-Mo alloy powder, Ni-Cr-Fe alloy powder, Ni-Cu alloy powder, Ni-P and Ni-Cr-P alloy powder, Ni-Cr-Mo-Fe Alloy powder, Ni-Cr-Mo-Si high wear-resistant alloy powder, Ni-Cr-Fe-Al alloy powder, Ni-Cr-Fe-Al-B-Si alloy powder, Ni-Cr-Si alloy powder, Ni- Cr-W based wear resistant corrosion resistant alloy powder.
-
nickel-based self-fluxing alloy powder is formed by adding an appropriate amount of B and Si to the nickel alloy powder. The so-called self-fluxing alloy powder is also called eutectic alloy, hard surface alloy, which is a series of powders formed by adding alloying elements (mainly boron and silicon) capable of forming low-melting eutectic crystals to nickel, cobalt and iron-based alloys. material. Commonly used nickel-based self-fluxing alloy powders are Ni-B-Si alloy powder, Ni-Cr-B-Si alloy powder, Ni-Cr-B-Si-Mo, Ni-Cr-B-Si-Mo-Cu, High molybdenum nickel base self-fluxing alloy powder, high chromium molybdenum nickel base self-fluxing alloy powder, Ni-Cr-WC based self-fluxing alloy powder, high copper self-fluxing alloy powder, tungsten carbide dispersed nickel base self-fluxing Alloy powder, etc.
The role of various elements in the alloy: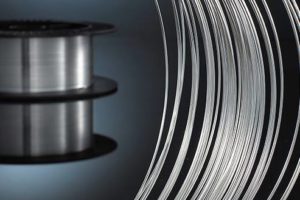
-
Role of boron and silicon: significantly reduce the melting point of the alloy, expand the solid-liquidus temperature zone, form a low-melting eutectic; deoxidation reduction and slagging function; harden and strengthen the coating; improve the process performance
-
Role of copper: improve the corrosion resistance of non-oxidizing acids
-
Role of chromium element: solid solution strengthening, passivation; improve corrosion resistance and high temperature oxidation resistance; excess chromium easily forms carbon carbide, chromium chromic hard phase with carbon, boron to improve alloy hardness and wear resistance Sex
-
Role of molybdenum element: large atomic radius, large distortion of the crystal lattice after solid solution, significantly strengthening the alloy matrix, improving the high temperature strength and red hardness of the matrix; cutting and reducing the network structure in the coating; improving gas resistance Eclipse, erosion capacity
Nickel-based precision alloy
-
Including nickel-based soft magnetic alloy, nickel-based precision resistance alloy and nickel-based electrothermal alloy. The most commonly used soft magnetic alloy is a permalloy containing about 80% nickel. Its maximum magnetic permeability and initial permeability are low, and its coercive force is low. It is an important core material in the electronics industry. The main alloying elements of nickel-based precision resistance alloys are chromium, aluminum and copper. These alloys have high electrical resistivity, low temperature coefficient of resistivity and good corrosion resistance for the fabrication of resistors. Nickel-based electrothermal alloy is a nickel alloy containing 20% chromium. It has good oxidation and corrosion resistance and can be used for a long time at 1000~1100 °C.
Nickel-based shape memory alloy
-
A nickel alloy containing 50% (at)% of titanium. Its recovery temperature is 70 ° C, shape memory effect is good. A small change in the proportion of nickel to titanium components allows the recovery temperature to vary from 30 to 100 °C. It is mostly used to manufacture self-expanding structural parts used in spacecraft, self-exciting fasteners used in the aerospace industry, artificial heart motors used in biomedical applications, and the like.
Shanghai HY Industry Co., Ltd has more than twenty years experience in kind of nickel alloy,Titanium alloy and cobalt alloy production.
When you want to know more about our products, please contact us:
https://hynickelalloy.com/product-center/